みなさんこんにちは。
ビジュアル系ガラス作家の高木基栄です。
あっというまに2017年も今日を含めて残すところあと2日。制作も年内ラストスパートっ
いつもは基本的に吹きガラスでの作品制作ですが、2月の個展ではキルンキャスト(ガラス鋳造)も組み合わせた作品を出したいと思っていたので学生の時以来のキルンキャストに挑戦中です。
※キルンキャスト(ガラス鋳造)=型を作ってそこにガラスを入れて電気炉で昇温、型通りの形にガラスを溶かし込む技法。チョコレートを100均とかで売ってる型に溶かし込む作業を思い浮かべてもらえるとわかりやすいです。
これをガラスでやってくよ◎
なので今回は吹きガラスではなくガラスを型に溶かし込むキルンキャストの紹介。
キルンキャストの工程紹介
原型制作
![]() |
![]() |
今回はスタイロフォーム(※発泡スチロールの硬めのやつ。型取り用の原型によく使用します)をスチロールカッターでいろんな形に切り出して原型にします。
原型作りの作業は粘土とか蝋を使ったりして形によって使い分けます。
最終的にガラスはこの原型の形になるので丁寧に作るとガラスになった後加工の作業が手間が少なく済みます◎
石膏型取り
![]() |
![]() |
スタイロフォームで作った原型に耐火石膏をかけて石膏の型を作ります。
※耐火石膏=900℃くらいまでの温度で使えるガラス鋳造の型を作るのに使う石膏です。
※2色に分かれているのは、最終的に型を分割して中のスタイロフォームを取り出すために型を分割できるようにしてあるから。
型の分割線をわかりやすくするために、片方の型を作る時に、石膏と水を攪拌する際にちょっとだけ墨汁を混ぜてます。
分割線がわかりづらい型なんかはこの方法だと一目で分割線がわかるので個人的にオススメ◎
型の分割線がわからずに型を壊してしまったのは学生時代のイイ思い出。。。
型を分割して中のスタイロフォームを取り出したら、最後に型を型の完成です◎
カマ入れ・ガラス溶解
![]() |
![]() |
型ができたらいよいよガラスを溶かす準備。カマの中に型を入れて、ガラスを詰めていきます。
型の体積×2.6〜2.8が必要なガラスの重さ。
ガラスが足らないと悲しいことになるので体積×3のガラスを入れます。
今回は夏のメンテナンスの際に出た緑色のガラスを使用◎
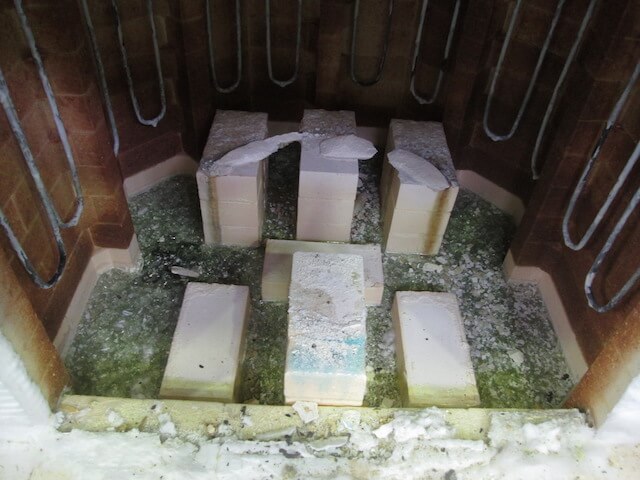
関連記事>>夏の汗まみれガラス工房メンテナンス記
今回のカマ入れの設定最高温度は880℃!
ゆっくり温度を上げていって、880℃を6時間キープします。
最高温度の時のカマの中はこんなカンジ。
ガラスの量は大丈夫そう(^^) 型も壊れることなく順調順調◎
最高温度の時にカマの扉を開けて、無事に中のガラスが溶けていることを確認したら490℃まで一気に温度を下げて、そこからは時間をかけてゆっくりとガラスを冷ましていきます。
※880℃からゆっくり冷ましてしまうとガラスが結晶化して不透明になっちゃう失透という現象が起こっちゃうので490℃までは一気に温度を下げて、常温まで一気に冷ましちゃうとガラスが割れちゃうので490℃からはゆっくり冷まします。ガラスってけっこう難しくてデリケート。。。
石膏型を外す
![]() |
|
無事にカマから出てきたガラス。。。
無事???
石膏を外して、キレイに水洗いして。。。
![]() |
![]() |
ヒビ入っとるし、失透しとるね!
2017年最後の仕事で失敗してたよ。。。(遠い目)
「うん!でもこの模様とかキレイでなんとか生かしたらキレイなカンジだよね!」
なんて優しい言葉で気を遣ってもらいながら、無言でそっと石膏のゴミを片付けて、ガラスを倉庫に安置してきました。。。
仕事納まらず
年内最後の作業が大失敗に終わり、手元に残ったのは失敗したガラスの塊。。。
ということで、制作延長戦が決定したので家でもできる作業を車に詰め込んで、ガラスと共に帰省しました♨
失敗した原因として考えられるのは、ガラスの種類がキルンキャストに合っていなかった。
もしくは、メンテナンスで出た緑色のガラスに色々不純物が不均一に溶け込んでてそれが原因でガラスにストレスがかかってヒビが入った。
もう個展にキルンキャストを使った作品を出すのはムリっぽいので、もう一つ取っておいた別の技法を使っての作品を出そうと思います!!
大晦日まで制作するよ〜2017年まだまだ頑張るよ〜
世の中には年末年始関係なく仕事してる人もたくさんいるからねっ!
おしまいっ
コメント